I wanna tell you a story....
When the build began, I understood that Mini's and Metro's had a 4"PCD (diagonal distance between wheel studs). When I was offered the Rover, I measured the PCD - 4" - great, I'll use Metro front hubs.
I duly sourced front hubs from a low mileage Rover Metro, put them in the corner of the workshop and forgot about them....
Big Mistake!!!!
A chance conversation with a 'Font of automotive knowledge' (whose Mastermind specialist subject is 'PCD's from 1872 to the present day') set me on edge. To the workshop.....
What we found:
1. The 'Rover' Metro uses a PCD of 95.6mm, unlike its A series predecessor.
2. the Rover 200/400 uses a PCD of 100mm, not 4" (101.6mm).
So nothing fits anything. B****x.
After long deliberation of the options, the difficult decision to ditch the Rover was made. Using a Rover Metro front subframe at the back was briefly considered but with the future supply of Rover parts in the balance, Uncle Henry's parts bin called.
The local tame scrappy is very keen to use my engine in his Banger racing car, so has offered me a deal on a Zetec-s engined Fiesta 1.25. This is a light, revvy engine that will fit in the chassis with no modifications. It also allows the use of standard 'Locost' suspension with Cortina Hubs at the front.
Stay tuned for 'Stripping the Donor part deux'...........
This site describes the construction of a home built, mid-engined car. First conceived in 1999 and inspired by cars such as the NCF Blitz and Onyx Tomcat. I finally began work this year(2005) with a friend, who is an Aircraft Engineer. Why Mistrale? Well, the author of 'A Year in Provence', described the Mistral as a "brutal, exhausting wind that can blow the ears off a donkey" - appropriate for a car with no roof, sides or windscreen. An 'e' was added as others have already used 'Mistral'
Monday, September 19, 2005
Catch up on the build so far
Building the Space frame
Step 1 was to purchase a sheet of 18mm MDF to use as a jig for the frames. The upper and lower planform were marked and holes drilled either side to accept a length of threaded rod. The cut tubes were put in place and clamped to the board using offcuts of plywood. This ensured that there was no distortion during the welding process. We then spent some time learning to weld, and here is the first Top Tip – MiG welding works MUCH better if you have gas in the bottle……..nuff said?


The top and bottom frames were then accurately positioned using a precision jig and the corner uprights cut to fit. Some time was spent ensuring an accurate fit prior to welding. As this was the first angled weld, a test piece was welded first – eventually with good results. However, when I tried on the chassis, it was awful! Nothing for it but to grind it off and start again. And again…Returning home in a foul mood, I kicked the cat and went to bed. Next day, same settings, nothing changed produced decent results. Doh!
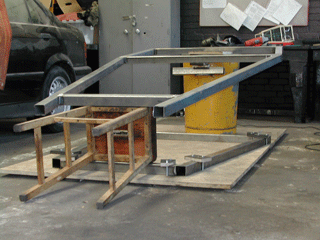

After the considerable effort cutting the uprights, for the diagonals we used a long length of paper to prototype the tube. This was wrapped around the tube then marked and cut. This gave excellent results with a good fit virtually straight away. Top Tip Two – Paper is SO much easier to cut than steel!
Step 1 was to purchase a sheet of 18mm MDF to use as a jig for the frames. The upper and lower planform were marked and holes drilled either side to accept a length of threaded rod. The cut tubes were put in place and clamped to the board using offcuts of plywood. This ensured that there was no distortion during the welding process. We then spent some time learning to weld, and here is the first Top Tip – MiG welding works MUCH better if you have gas in the bottle……..nuff said?


The top and bottom frames were then accurately positioned using a precision jig and the corner uprights cut to fit. Some time was spent ensuring an accurate fit prior to welding. As this was the first angled weld, a test piece was welded first – eventually with good results. However, when I tried on the chassis, it was awful! Nothing for it but to grind it off and start again. And again…Returning home in a foul mood, I kicked the cat and went to bed. Next day, same settings, nothing changed produced decent results. Doh!
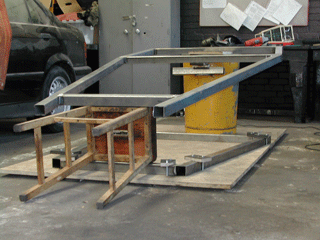

After the considerable effort cutting the uprights, for the diagonals we used a long length of paper to prototype the tube. This was wrapped around the tube then marked and cut. This gave excellent results with a good fit virtually straight away. Top Tip Two – Paper is SO much easier to cut than steel!

Sunday, September 11, 2005
Stripping the Donor Car

The donor car was a 1990 Rover 416GTi that was purchased from a friend for the princely sum of £10. It had failed its MoT because of a small area of rust next to a suspension mount - no problem to fix once removed from the car! Other that this, the car had had much attention and money lavished upon it including nearly new back brakes.
The first evening was a bit like a feeding frenzy. With the help of two friends, most of the under bonnet connections were undone, along with the front crossmember - all of this taking about an hour. We decided to strip the car outside to ease disposal of the bodyworf once it had no wheels. On the second night, working alone, I disconnected the steering column, pedals and gearchange - again about an hour before the light faded. On the final night, a friend helped lift the front of the car with an engine hoist, and prop it up. A trolley was then wheeled under the engine and gear box. The final mounts were undone and the car lifted off the engine/trolley assembly!

We then returned to remove various other parts from the car. The back axle and rear uprights were removed as a complete unit - in case anything proved useful! Next followed the fuel tank, filller neck and the remains of the exhaust. The wiring loom followed after a very hot evening of work and finally, an angle grinder was taken to remove the thick walled bushed that the two fornt cross members bolted into. The full leather interior had already been removed and has been put aside - if it is not used, e-bay calls!
Subscribe to:
Posts (Atom)